Gli elementi in metallo e alluminio possono essere sottoposti ad apposite lavorazioni, procedimenti particolari con i quali è possibile conferire nuove proprietà ai componenti in base alle esigenze applicative. Ogni soluzione consente di ottenere performance specifiche, migliorando le capacità della struttura in termini di resistenza, durabilità e utilizzo. Vediamo quali sono i principali rivestimenti e trattamenti superficiali per i metalli disponibili.
Anodizzazione pura: caratteristiche e vantaggi
Come segnalato sul sito Argos-st.com, impresa che si occupa di soluzioni avanzate per i trattamenti e i rivestimenti superficiali, una tecnica molto apprezzata per i metalli è l’anodizzazione dura. Questo processo prevede il passaggio dei manufatti metallici in vasche sottozero con l’applicazione di corrente, per ottenere la formazione di uno strato di ossido duro sul rivestimento della struttura metallica.
L’ossidazione anodica a spessore permette di aumentare le proprietà del materiale in termini di resistenza all’usura e alla corrosione, inoltre consente di conferire al manufatto capacità antiattrito, un discreto isolamento e maggiore stabilità termica. Le sue applicazioni sono innumerevoli, infatti trova impiego nell’industria alimentare, farmaceutica, automobilistica, chimico-farmaceutica e aeronautica.
Cos’è l’anodizzazione e quali sono le applicazioni
Un altro tipo di trattamento è l’anodizzazione, una tecnica che rende possibile proteggere i metalli attraverso il processo di ossidazione. Viene usata appena sugli elementi in alluminio, con lo scopo di formare uno strato superficiale di ossido di alluminio tramite la reazione che avviene tra l’ossigeno e il metallo, con uno spessore da 5 a 20 micron e la possibilità di ottenere un rivestimento neutro o colorato.
Il procedimento è realizzato con un metodo che prevede tre passaggi, il trattamento preliminare, l’ossidazione anodica e le finiture, per garantire alla struttura in alluminio performance superiori nello scorrimento e nella resistenza alla corrosione e all’usura. Inoltre i pezzi trattati vantano un aspetto valorizzato, con una resa estetica di altissima qualità. Le applicazioni degli elementi anodizzati sono numerose, dal settore petrolchimico a quello automobilistico.
Come funzionano i rivestimenti con nichelatura chimica
In molti campi applicativi sono richieste capacità elevate di resistenza alla corrosione, per evitare il deterioramento dei metalli e ottenere standard di qualità elevati, aumentando la durata dei manufatti metallici e usufruendo di migliori prestazioni operative. I rivestimenti con nichelatura chimica trovano spazio in ambiti come l’industria petrolchimica, aeronautica e automobilistica, per beneficiare di vantaggi in termini di riduzione dei costi di manutenzione e incremento dell’efficienza produttiva.
In questo caso esistono diverse opzioni disponibili, come il processo Niploy per realizzare un rivestimento uniforme anche su elementi con geometria complessa, oppure con sistema Cheniflon utilizzando particelle di PFTE per conferire al materiale proprietà antiaderenti e una maggiore scorrevolezza. La nichelatura chimica può avvenire anche con la combinazione di carburo di silicio, per usufruire della massima durevolezza, oppure con rivestimento ad alto fosforo per aumentare le performance di saldabilità e resistenza all’usura.
Le proprietà dei rivestimenti a base di polimeri
Il rivestimento dei metalli può essere realizzato attraverso l’uso di appositi polimeri, una tecnica che può essere adoperata su numerosi materiali come i metalli, la fibra di carbonio e perfino la plastica. Ad esempio è possibile applicare polimeri di Teflon, per conferire ai materiali capacità elevate di antiaderenza, resistenza chimica e scorrevolezza, caratteristiche molto apprezzate nell’industria alimentare, farmaceutica e medicale.
Per una maggiore protezione chimica dei materiali è possibile optare per un rivestimento a base di fluoropolimeri, con la possibilità di tutelare l’elemento metallico dall’azione delle sostanze più aggressive, con applicazioni anche in ambiti operativi complessi. In base alla tipologia e alla tecnologica del rivestimento polimerico si possono ottenere alte performance antiattrito, una migliore lubrificazione, una barriera contro gli agenti chimici, oppure un maggiore protezione contro la corrosione.
Le diverse soluzioni per i rivestimenti termospruzzati
Per formare un rivestimento sui materiali metallici esiste anche il procedimento della termospruzzatura, il quale abbinato ai processi di spray coating consente di ottenere vantaggi importanti in termini di scorrimento, resistenza all’abrasione e antiaderenza. Per esempio, i rivestimenti in ceramica sono ideali per ottenere un maggiore isolamento elettrico, aumentare la durevolezza e migliorare le capacità di resistenza termica e protezione contro l’usura.
I rivestimenti al carburo di tungsteno, invece, assicurano prestazioni eccellenti per la resistenza all’usura e la durezza del materiale, con applicazioni che vanno dal campo militare alla produzione di attrezzature. Inoltre è possibile optare per un rivestimento in zinco, un trattamento con termospruzzatura perfetto per proteggere i manufatti e aumentarne la resistenza alla corrosione, con utilizzi frequenti nelle attività legate al packaging.
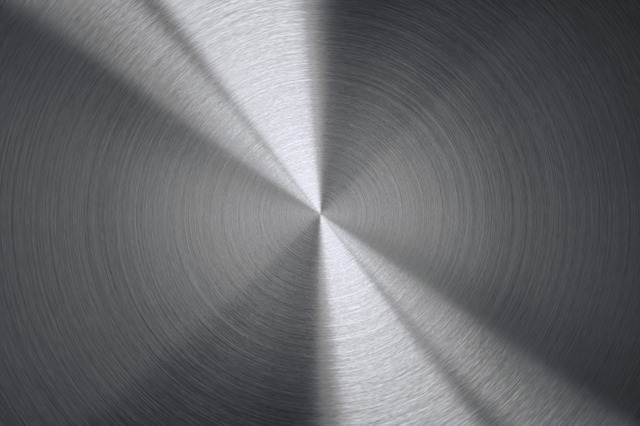